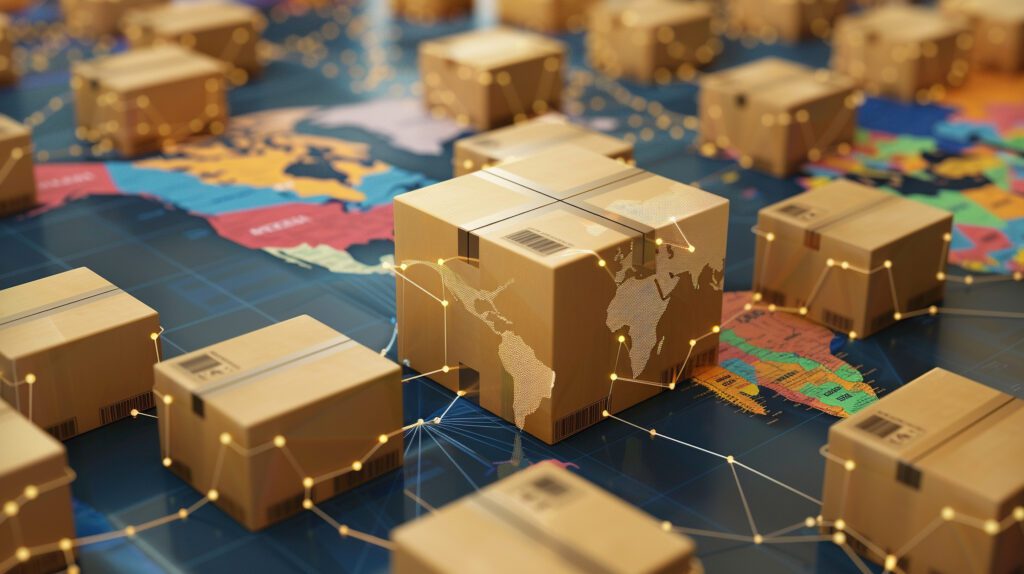
In the world of supply chain and logistics, effective inventory management is crucial to maintaining a smooth operation and ensuring customer satisfaction. Inventory management becomes even more complex when dealing with multi-echelon systems, where multiple layers of inventory are maintained at different stages in the supply chain. The term “multi-echelon” refers to managing inventory across various levels of a supply chain, such as manufacturers, distribution centers, and retailers, where inventory decisions at one level impact the overall performance of the system.
The fragility of global supply chains
The COVID-19 pandemic has fundamentally altered the global supply chain management landscape, exposing vulnerabilities in global supply chains and highlighting the need for more resilient inventory management practices. The pandemic-induced disruptions led to severe shortages of essential goods, including baby formula and diapers, as supply chains were crippled by lockdowns, factory closures, and transportation bottlenecks.
The shortages of baby formula and diapers during the pandemic underscored the limitations of traditional inventory management systems, which struggled to cope with the unpredictable demand spikes and supply chain disruptions. Panic buying and hoarding further exacerbated the situation, leaving retailers unable to keep up with demand.
Another significant event that recently highlighted the fragility of global supply chains was the blockage of the Suez Canal in March 2021. When the Ever Given, a massive container ship, became lodged in the canal, approximately 12% of the global trade was halted for several days. This incident caused widespread disruptions, delaying shipments of critical goods and leading to shortages and production delays across various industries.
These events have catalyzed a shift in how retailers approach inventory management and Multi-echelon Inventory Optimization systems have become essential in building more resilient, adaptive supply chains that can better predict demand, optimize stock levels, and respond dynamically to unforeseen disruptions.
Multi-echelon inventory management (MEIM) involves addressing stock replenishment and allocation challenges across different layers to minimize total costs while ensuring high service levels. In classic models, inventory is often managed using traditional mathematical methods such as the Economic Order Quantity (EOQ), base-stock models, or safety stock formulas. However, as businesses become more globalized and complex, these classical models often fall short when dealing with dynamic market conditions, erratic demand patterns, and unpredictable supply chain disruptions.
This is where data science and artificial intelligence (AI) come into play. With the advent of AI-powered algorithms, machine learning, and predictive analytics, businesses can enhance their traditional inventory models to be more robust, responsive, and agile, making them better suited for today’s dynamic business environment.
What is multi-echelon inventory management?
In simple terms, multi-echelon inventory management involves optimizing inventory levels across multiple layers in a supply chain. Each echelon, or level, can consist of:
- Manufacturers: Where raw materials or components are converted into finished products.
- Distribution Centers: Warehouses that hold inventory for regional markets.
- Retailers: The final point in the supply chain where products are made available to end customers.
Managing inventory in such a multi-layered system presents unique challenges. The goal is to ensure that each echelon holds the optimal amount of stock to minimize both stockouts (lost sales due to unavailable products) and excess inventory (which ties up capital and incurs holding costs).
To achieve this, businesses rely on classic inventory models like the Economic Order Quantity (EOQ) and reorder point formulas, which work well for simpler systems. However, these methods assume steady demand and fixed lead times—assumptions that are rarely valid in today’s volatile market conditions.
Classical multi-echelon inventory management
Multi-echelon inventory management (MEIM) refers to the process of managing inventory across multiple stages or “echelons” within the supply chain. These echelons can include suppliers, warehouses, distribution centers, and retail locations. The objective is to minimize total inventory costs while maintaining desired service levels across the entire network.
Key concepts
- Echelon Stock: This represents the total inventory available at a particular stage, including upstream inventories. The goal is to optimize this stock across the entire network.
- Reorder Points and Lead Times: Each echelon has a reorder point, calculated based on expected demand and lead times, which drives replenishment orders from upstream echelons or suppliers.
- Demand Propagation: Demand at the retail level propagates upstream through the supply chain. Each stage accumulates demand from downstream stages, resulting in a need to balance supply and stock at each echelon.
Inventory policies
The classical policies in MEIM are often based on deterministic or stochastic demand models. Common policies include:
- Base Stock Policy: This policy ensures that inventory is replenished to a certain level after every demand cycle. It is optimal for minimizing holding and shortage costs under certain assumptions.
- Order-Up-To (OUT) Policy: In this policy, the inventory is replenished up to a predetermined level whenever it falls below a reorder point. It is commonly used when demand is variable but follows a known distribution.
Classical approaches to MEIM rely on simplifying assumptions. For example, the classic base-stock model assumes that inventory at each echelon is reviewed continuously, and orders are placed whenever the inventory level drops below a certain threshold. The reorder point is calculated based on the expected demand during lead time and a safety stock that buffers against variability in demand or lead time.
For a single-echelon system, the base-stock level S is determined as:
S=μ⋅L+Z⋅σ⋅ L
Where:
μ is the average demand rate per period,
L is the lead time,
Z is the z-score corresponding to the desired service level,
σ is the standard deviation of demand per period.
In a multi-echelon context, managing the inventory becomes significantly more complex. The classic Clark-Scarf model for two echelons introduces the concept of decentralized control versus centralized control. In decentralized control, each echelon makes independent decisions, leading to inefficiencies such as the bullwhip effect—a phenomenon where small changes in customer demand lead to larger swings in demand at upstream echelons. Centralized control, on the other hand, involves making coordinated decisions across all echelons to minimize total costs.
The Clark-Scarf model minimizes the total cost of the system by jointly optimizing the ordering decisions across multiple echelons. The basic problem is formulated as a dynamic program where:
- C(i,j) is the total cost of the system if we order i units at echelon 1 and j units at echelon 2.
- D is the demand distribution.
- The objective is to minimize the expected total cost across all echelons.
While classical models like this provide a starting point, they often become impractical for real-world applications due to their reliance on restrictive assumptions.
Challenges of classical MEIM Models
- Demand Variability: Classical models often assume constant demand, but in reality, demand fluctuates due to seasonality, promotions, or economic conditions. The models fail to dynamically adjust to these changes.
- Lead Time Uncertainty: Lead times are assumed to be fixed in traditional models. However, in practice, lead times can vary due to transportation delays, supplier issues, or production bottlenecks.
- Inventory Centralization: Classical models are decentralized by nature, leading to suboptimal decisions that increase costs across the supply chain.
- Data Sparsity: Traditional models rely on historical data for forecasts, but in many cases, data is either insufficient or irrelevant due to rapid changes in business conditions.
Unlocking the future of inventory optimization: The game-changing impact of data science and AI on multi-echelon management
Data science and AI techniques offer a revolutionary approach to overcoming the limitations of classical MEIM models. By incorporating real-time data, advanced machine learning algorithms, and predictive analytics, businesses can build smarter inventory systems that dynamically respond to changing market conditions.
1. Demand forecasting with machine learning
Accurate demand forecasting is critical for effective inventory management. Classical models rely on historical averages and simple forecasting methods like exponential smoothing. However, these methods are often inadequate for handling volatile or non-stationary demand patterns.
Machine learning models can significantly improve demand forecasting by incorporating a wider range of variables, including:
- Historical sales data,
- Seasonality,
- Promotions,
- External factors such as economic indicators, weather data, and social media sentiment.
Popular machine learning models for demand forecasting include:
- Random Forests: A decision-tree-based ensemble method that accounts for complex, non-linear interactions between input variables.
- Gradient Boosting Machines (GBM): Another tree-based method that can handle highly complex data structures.
- Neural Networks: Particularly useful for capturing non-linear relationships and temporal dependencies, making them ideal for time-series forecasting.
For instance, a neural network model might predict demand yt at time t as:
y_t = f(x_t, x_{t-1}, \dots, x_{t-n})
Where xt represents various factors like historical sales, pricing, and marketing efforts at time t.
By continuously retraining these models on new data, businesses can update their forecasts in real-time, ensuring that replenishment decisions are based on the most up-to-date information.
2. Inventory optimization using reinforcement learning
Reinforcement learning (RL) is a powerful AI technique that allows inventory systems to learn optimal policies through trial and error. In an RL framework, an agent (the inventory manager) interacts with an environment (the supply chain), taking actions (e.g., ordering inventory) and receiving rewards (e.g., minimizing holding costs or stockouts).
The goal is to learn an optimal policy π\piπ that maximizes the expected cumulative reward. Mathematically, this is expressed as:
\pi^* = \arg \max_{\pi} \mathbb{E} \left[ \sum_{t=0}^{T} \gamma^t r_t \right]
Where:
- rt is the reward at time step t,
- γ is the discount factor,
- T is the time horizon.
RL is particularly effective in multi-echelon systems where the complexity of inventory decisions grows exponentially with the number of echelons. By training RL algorithms, businesses can learn optimal replenishment policies that account for lead time variability, demand uncertainty, and interdependencies between echelons.
3. Safety stock optimization with AI
In classical models, safety stock is calculated using fixed safety factors based on demand variability. However, this approach often leads to overstocking or understocking. AI can help optimize safety stock levels by dynamically adjusting the buffer based on real-time data.
Using a combination of machine learning and statistical models, AI systems can continuously monitor lead times, demand patterns, and service levels to recommend optimal safety stock. For instance, a stochastic optimization algorithm might minimize the expected cost of stockouts and holding inventory:
\min \mathbb{E} \left[ C_{stockout} \cdot P(stockout) + C_{holding} \cdot I \right]
Where:
- Cstockout is the cost of stockouts,
- P(stockout) is the probability of a stockout,
- Cholding is the cost of holding inventory,
- I is the inventory level.
This real-time adjustment ensures that businesses maintain just enough inventory to meet demand without over-investing in excess stock.
4. Supply chain resilience through PMI analytics
In an era where supply chain disruptions have become commonplace—due to factors like natural disasters, geopolitical tensions, or global pandemics—supply chain resilience is more important than ever. Analyzing Purchasing Managers’ Index (PMI) data provides early insights into potential supply chain disruptions by signaling shifts in economic activity. A declining PMI suggests reduced production and longer lead times, allowing businesses to adjust inventory levels and secure alternative suppliers in advance. By tracking PMI trends globally, companies can better anticipate and mitigate supply chain risks, ensuring greater resilience and continuity in operations. Furthermore, analytics on PMI data powered by AI can help companies anticipate and mitigate disruptions by analyzing vast amounts of data.
AI algorithms can predict the likelihood of supplier delays by analyzing various factors, such as:
- A supplier’s historical performance during geopolitical or economic events.
- Potential transportation bottlenecks along key shipping routes.
- Weather patterns that could impact the production of agricultural raw materials, e.g. cotton.
These insights enable businesses to proactively address potential disruptions in their supply chain by adjusting safety stock levels, rerouting shipments, or finding alternative suppliers.
Conclusion
Multi-echelon inventory management is a complex but critical task in today’s global supply chains. While classical models provide a foundation, they are often insufficient to handle the complexities of modern supply chains. By incorporating data science and AI, businesses can enhance the robustness and agility of their inventory systems, making them more responsive to dynamic market conditions.
Advanced demand forecasting, reinforcement learning, and real-time optimization can transform MEIM from a reactive, siloed process into a proactive, data-driven function that ensures high service levels, minimizes costs, and improves overall supply chain efficiency. The future of multi-echelon inventory management lies in the integration of classical models with cutting-edge AI techniques that can navigate the intricacies of today’s fast-paced, interconnected world.
Você conseguiu transformar um tema potencialmente complicado em algo acessível e fácil de entender, sem perder profundidade.