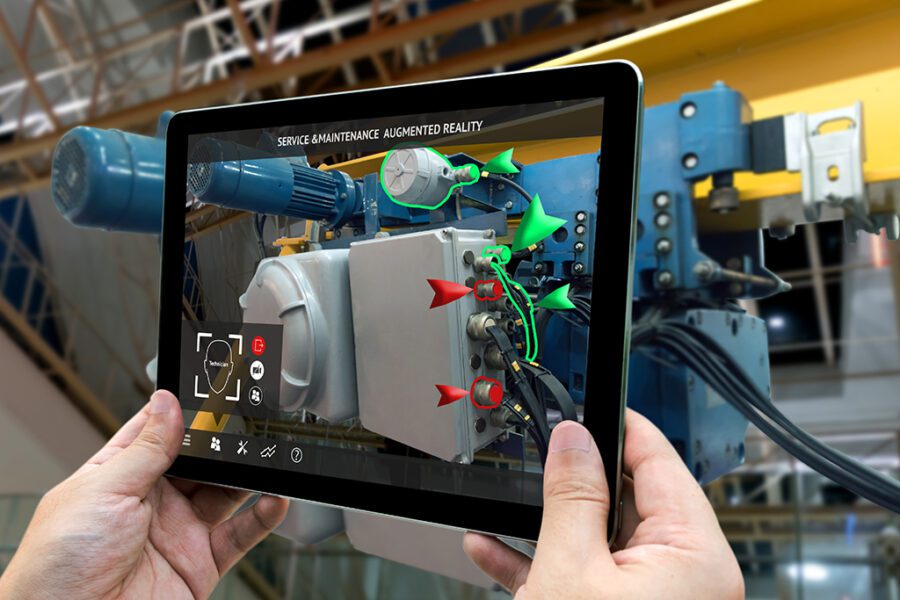
Despite the technological breakthroughs in the advent of Industry 4.0, manufacturers seem to have taken a more gradual approach to adoption. In 2020, less than 30 percent of the industry considered themselves extensive users of advanced integrated tools and processes. The pandemic, however, brought out an unprecedented need to explore opportunities that make manufacturing systems more resilient. Software as a service (SaaS) is one of the most practical functionalities illustrating the ways in which technology can improve existing procedures.
What is SaaS?
Whether they are aware or not, anyone using a computer is employing some form of a computer program or software. There is a wide variety of categories to describe software, one of which is the way they are accessed or obtained.
The key differentiator betweenSaaS and traditional software is that SaaS is a web-based program accessible through the internet -so, installing software no longer requires a physical device such as a compact disc or a thumb drive. Customers or prospective users only need an internet connection and the proper hardware specifications.
Software users can think of the internet as a direct link to their service provider. The connectedness of a user to the provider allows for a higher degree of adaptability. For instance, it is generally easier to upgrade or downgrade a subscription plan as the needs of a company change. The maintenance and infrastructure costs of operating a program typically sit with the provider. Any updates or patches are also available through the internet without requiring a physical medium.
Remember – SaaS provides the game-changing opportunity of making software available to virtually anyone. As you might imagine, the applications are limitless. Any perceivable industry requiring software can benefit from such an arrangement.
Data-Driven Manufacturing
Before we dive into how SaaS impacts manufacturing practices, it helps to look into the role of data in driving decisions. It goes without saying that equipment reliability and the capacity to perform work are essential for any manufacturing company. However, what is not as obvious are the concrete actions that a company needs to take to achieve optimal productivity. An emerging trend among industry giants is to invest in Smart Maintenance practices to perform massive data crunching.
With unplanned downtime costing manufacturers nearly $50 billion, 42% of which is due to asset failure, the incentive to enhance maintenance procedures is remarkable. Maintenance strategies utilizing artificial intelligence and machine learning aim to get ahead of a failure event. By analyzing significant amounts of data, these technologies can predict the condition of an asset and prescribe required action.
The more conventional preventive maintenance (PM) concept similarly aims to service equipment before any significant incident occurs. PM, however, falls short in the accuracy of the timing when scheduling tasks. A poorly designed PM strategy runs the risk of performing nonvalue-adding work. Predictive maintenance that uses AI algorithms to analyze data can streamline maintenance resources to execute tasks more purposefully. Investing in tools that allow for more prescriptive actions pays back by eliminating waste without sacrificing equipment reliability.
SaaS in Maintenance
Improvements in maintenance effectiveness and efficiency heavily rely on data available in a form that lends itself to analysis. Depending on the size of operations and the number of active equipment or assets of a facility, gathering and managing it manually can be exceedingly challenging. The good news is that there are existing programs dedicated to assisting asset maintenance management. Additionally, modern versions of these types of software are available as a service.
Enterprise Asset Management (EAM) software has to be at the top of the list of the most appropriate tools for the job. It provides a comprehensive view of maintenance management and in-depth insights towards asset performance improvements. Imagine having information about all of the company’s critical pieces of equipment, across multiple factories, in one central location.
On top of that, modern EAM programs typically come in the form of a SaaS so companies have the option to subscribe to a level of service that fits their immediate needs. When the necessity for an increased number of subscribers or expanded functionalities arises, software updates should be readily available through the internet.
For example, if a facility were to implement an advanced maintenance strategy, such as prescriptive maintenance, it would need to have an extensive view of several pieces of equipment at all times. Whenever there is a process change or a machine addition, relevant maintenance software will potentially require an update to upgrade capacity. In such cases, a more adaptable software becomes far more crucial to keeping up with the needs of ever-changing times.
Turning Insights into Actions
With the importance of maintenance and the beneficial functionalities of available SaaS tools, it makes perfect sense to bring these elements together towards a common goal. The increased connectivity offered by SaaS sets it apart from traditional software, and SaaS can pave the way for turning insights into actions more efficiently for the very same reason.
Applications that maximize internet connectivity allow a more seamless approach to storing and integrating data from various systems. In maintenance, these systems are vital to instantaneously finding asset issues by leveraging real-time data from throughout the facility.
EAM, for instance, aims to broaden the view to encompass processes within the entire enterprise. In the same way that SaaS allows users to connect with the provider, a company-wide EAM program can incorporate information from various departments. It starts with identifying maintenance requirements at the equipment level while gathering relevant information about asset performance. Such data can then inform accounting decisions and calculations to achieve the desired return on investment. Moreover, it provides supply chain processes with invaluable insights about the best timeframe to bring in the required inventory when needed.
Conclusion
If there is one takeaway about these current times, it would most likely have to do with the importance of adaptability and finding ways to do things better. While it may sound like a daunting challenge, modern technologies provide effective alternatives that are more affordable in the long run. Tapping into these more intelligent ways of working makes it easier to transform data-driven insights into actionable efforts.
Author’s bio: Eric Whitley has 30 years of experience in manufacturing, holding positions such as Total Productive Maintenance Champion for Autoliv ASP, an automotive safety system supplier that specializes in airbags and restraint systems. He is also an expert in lean and smart manufacturing practices and technologies. Over the years, Eric has worked with all sectors of industry including Food, Timber, Construction, Chemical and Automotive to name a few. Currently, he’s a part of the L2L team.