Companies today are striving to maximize product quality, efficiency, and security through effective maintenance practices and the care of equipment. In light of Industry 4.0’s advent, manufacturers are increasingly turning to digital twin technology as a predictive and management tool for complex assets commonly found within industrial settings. These are replacing the time-consuming and expensive physical prototyping methods with an economical, secure way of safeguarding critical assets.
Digital twin technology is experiencing rapid expansion within manufacturing industries, where its market is projected to surpass $6 billion by 2025. This growth demonstrates its transformative effect and inspires widespread adoption by various industries worldwide.
Understanding the digital twin concept
David Gelernter first proposed the idea of digital twins in his book ‘Mirror Worlds’, and Michael Grieves later applied it to manufacturing processes. John Vickers of NASA popularized the term “digital twin” for use with space capsule and spacecraft simulation testing purposes in 2010.
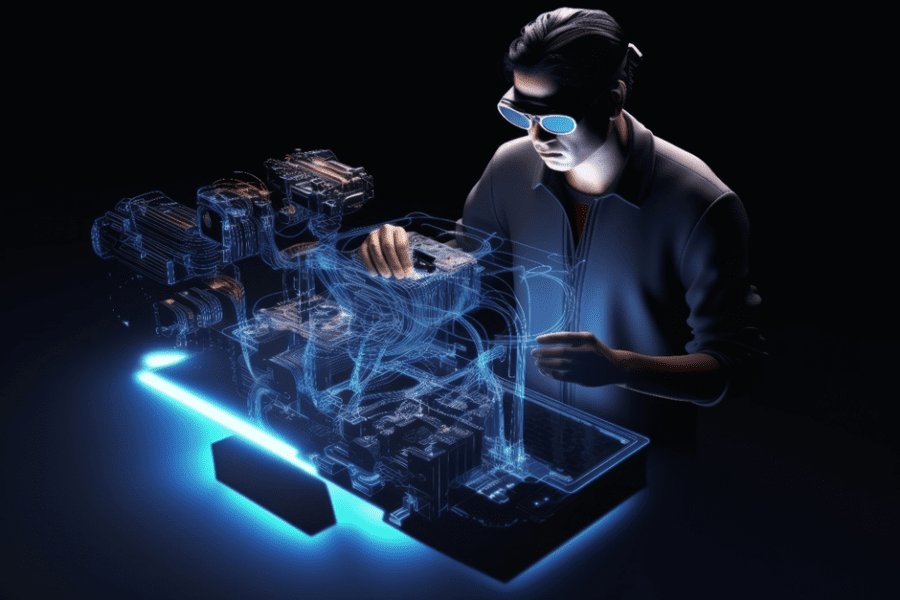
Simply defined, a digital twin is a virtual representation of physical objects, systems or processes that is designed to accurately replicate its counterpart in physical reality. One prominent example is Google Maps – an online representation of Earth that provides real-time traffic data in order to optimize commute routes.
Establishing a digital twin requires collecting data from sensors attached to physical assets, and using that data to build an exact virtual representation. By providing such insight into real-time asset behavior in its operational environment, digital twins enable users to maximize performance, anticipate maintenance needs, and prevent costly failures.
How digital twins work
To illustrate how a digital twin works, consider a wind turbine equipped with sensors to monitor key aspects of its performance such as temperature, energy output, and weather conditions. Once collected by these sensors, their data feeds into a digital twin where simulations and analyses allow the identification of performance issues and patterns that emerge, as well as suggested improvements that might benefit.
Manufacturers frequently rely on solutions like Asset Performance X to optimize manufacturing processes and boost asset performance. Built on OmniConnectTM Data Cloud, this platform features pre-built models based on both physics and machine learning that make optimizing asset performance simpler than ever. Users can easily select an asset type, enter design data, map live streams, and calculate KPIs automatically – providing an in-depth real-time view of asset performance that facilitates informed decision-making.
Benefits of digital twins in manufacturing
Asset operation efficiency is central to productivity and cost management for industrial and manufacturing enterprises. Yet inefficiencies in plant operations often represent major impediments to success, from unscheduled maintenance costs and unpredictable asset performance. This leads to reduced equipment lifespan and rising energy bills.
Digital twins as a tool help manufacturers overcome such hurdles by offering invaluable insight into plant performance allowing operators to anticipate any issues as soon as they arise. Let’s explore certain pros of adopting digital twin technology:
- Risk analysis: Inefficient running of a plant leads to the business facing challenges like unplanned downtime, inability to monitor and control asset performance, and reduced overall equipment lifespan. It is imperative to enable efficient operations of equipment and assets to maximize productivity and lower costs. Digital twins enable manufacturers to assess risks accurately so that any potential issues are identified and addressed before they become troublesome.
- Predictive and preventative maintenance: Unscheduled downtime can be costly. Digital twins help mitigate this cost by using historical data analysis to anticipate component failure or other issues and allow timely maintenance to ensure continuous production and timely repairs.
- Process and production optimization: Digital twins enable manufacturers to accurately predict product quality and make informed decisions regarding process improvements and material upgrades, helping ensure consistent large-scale production that matches specifications exactly. Furthermore, digital twins help identify more efficient production methods that reduce energy and material usage while meeting sustainability goals.
- Real-time asset monitoring: Digital twins offer real-time insights into physical assets, enabling manufacturers to make quick, informed decisions more quickly and extend equipment lifespan. With ongoing asset health monitoring capabilities, manufacturers are also better able to make more informed decisions regarding physical asset purchases and maintenance decisions.
Real-world applications of digital twins
Digital twin technology is ideal for manufacturing environments involving complex, large-scale assets that need continuous access to data. Industries from aerospace to energy have already taken advantage of digital twins to optimize their operations.
Asset Performance X has recently been used to create a digital twin for a renewable power plant in Morocco, providing insights that have allowed its operators to make data-driven decisions and increase power production by adjusting operational philosophy and bypassing feedwater heaters during low load times.
Digital twins in major industries
Digital twins are revolutionizing asset-intensive industries by providing an integrated physical and digital view of assets, equipment, processes, and facilities. As digital twin technology progresses further, its potential applications become endless as new features and capabilities emerge that further increase manufacturing efficiency and productivity.
To ensure that your manufacturing facility is equipped with modern technology needed for maximum optimization, talk to us.
Hi,
Great Blog! Your insights are spot on Embracing digital twin technology: A smarter approach to manufacturing. I especially appreciate your points. It’s evident you’ve done your research. Keep up the excellent work! Looking forward to reading more from you.