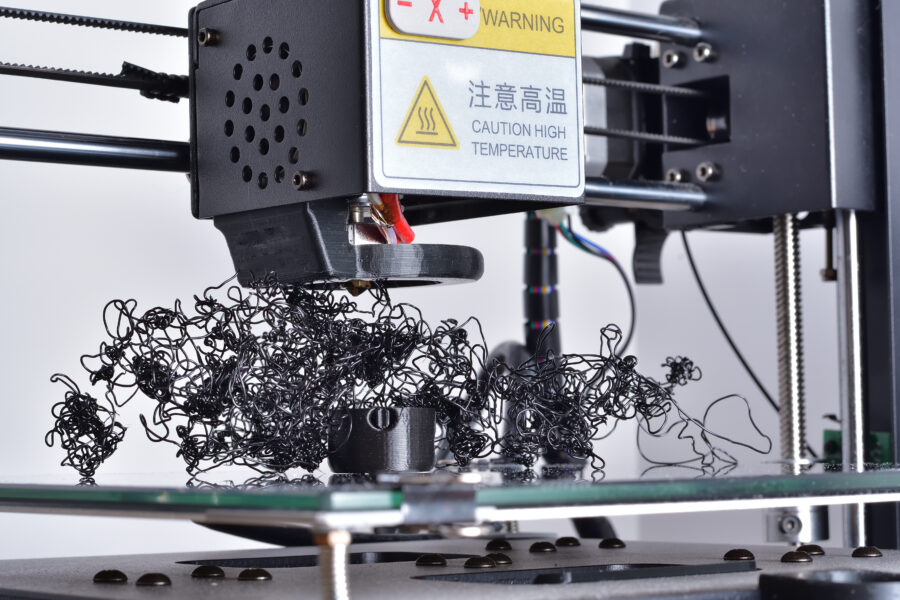
In the last few years, consumer-level 3D printing hardware has been gaining popularity in the hobby space, and it’s easy to see why. The ease of accessible or free CAD software, in conjunction with the culture of hosting custom-designed models for free, has given the niche tool a broad appeal. The gold standard for entry-level 3D printers even just a few years ago was the basic Ender 3, which boasted a modular design and relatively good out-of-the-box performance. Now, some companies are introducing products that trade modularity in favor of advanced automatic calibration, camera sensors, and even LiDAR scanners and AI print failure detection. The increasing user-friendliness and self-correcting machine behavior transformed them from an engineer’s toy to a device marketed even towards children.
AI visual analysis use cases
One common anecdote for anyone who has been printing for a long time is to watch your printer like a hawk while the first layer is laid down, and periodically thereafter. Perfectly dialing in the settings for not only a clean first layer but also one that is strongly adhered to the print bed is a skill gained through trial and error. More advanced printers are starting to come packaged with camera systems that replace the vigilant watcher that can analyze the material output while also correcting it in real-time.
First-layer inspection and real-time monitoring
The first layer is a vital part of any print. It determines if the object is firmly planted for the duration of the print, which could cause issues later down the line if it were to come loose. Not only that, the first layer is also the thinnest layer consisting of only a single extrusion. Any irregularities can be detected and diagnosed before hours of time and potentially hundreds of grams of plastic filament are wasted.
Even with a perfect first layer, issues with bed adhesion can still arise from a variety of other places, leading to what’s commonly referred to as a “spaghetti failure.” This type of failure gets its name from the tool head continuing to extrude as normal, but the model underneath no longer being stable, resulting in a messy string of filament that looks like a plate of spaghetti. In systems that do not have real-time monitoring, the printer would continue to execute the move commands until it finished the expected print job, but in systems that utilize real-time monitoring with AI-based detection, they can quickly determine that the tool head is producing a spaghetti failure and pause or fully stop the print job before the failure becomes too costly.
Material flow analysis
Another aspect of the 3D printing hobby is material flow calculation. Each type of plastic that one can buy behaves differently, and even the same type can vary from manufacturer to manufacturer, and even printer to printer. Calculating material flow is simply calibrating the material extrusion multiplier until ir conforms with an expected outcome. Too much material flow and the surface becomes rough as the excess material expands to find a space to occupy. Too little and there are gaps between extruded lines of material, compromising the structural integrity and surface finish.
Advanced printers can extrude a single line and use advanced sensors such as LiDAR scanners to measure the width of an extrusion compare it to an expected value, and scale the material flow multiplier accordingly. These dynamic adjustments can be done automatically and in real-time, removing the need for a human to measure and interpret the results. As environmental circumstances change, the flow will also need to be recalculated, so an automated computer process that will continuously monitor the output for changes in flow c an adjust accordingly.
Dimensional accuracy
One often overlooked aspect of 3D printing is dimensional accuracy. 3D printers run on commands known as G-code, similar to CNC machines and other industrial tools. In a sense, all this code does is issue commands for where to move, at what speed, and how to get there. It has no sense of “where” the tool head is unless it starts from a home position, but depending on the machine calibration, any movement from that point on is entirely dependent on the accuracy of the machine.
For example, if the tool were to start at the known home position in the center of the print bed and create a line 20mm long to the left, the g-code would have to tell the stepper motors how much to turn to move the tool head 20mm to the left rather than telling the tool head how to move. AI-driven visual analysis can measure the actual extruded line path compare it to the expected 20mm length and adjust the calibration parameters for the X Y and Z dimensions. In the past, this would have to be done as a manual process by printing a known-sized object, measuring the printed object, and adjusting accordingly.
Conclusion
While the current uses of AI in 3D printing hardware are mostly removing tedious calibration and monitoring, there are potential uses in the future that could improve the experience even further. By utilizing the data already collected in the above use cases, printers could theoretically predict when maintenance on specific parts is due based on print errors. On the software side, there is already some development using AI to assist in designing models and optimizing structures. Generative design and topology optimization powered by AI algorithms create lightweight yet strong structures by removing unnecessary material, making designs more efficient. As AI continues to evolve, it can predict and suggest design improvements based on real-world data to enhance the functionality of the part, and the ease of printing.