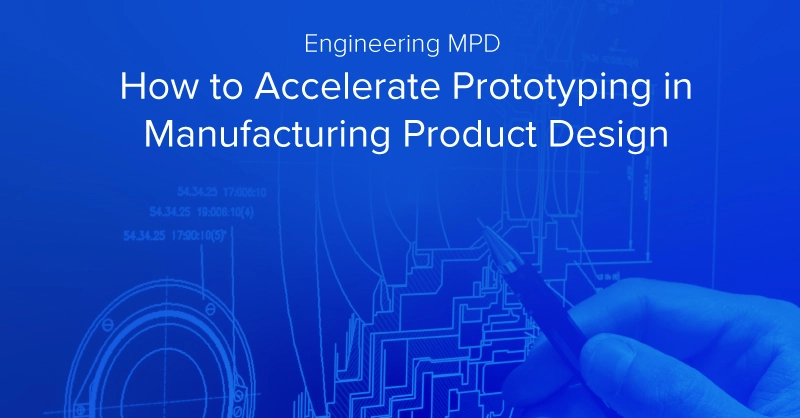
Introduction
Prototyping is an essential step in product design that ensures that everyone from designers to developers has a shared understanding of the product’s functions and appearance. Providing clear direction for the next stages of the product development process only starts at the prototype.
The ability to quickly move from concept to prototype to the final product makes an enormous difference in maintaining control of various markets. It plays a crucial role in communicating with the team and providing a tangible way to demonstrate the product’s potential.
Prototyping can be gruesome, with endless iterations until a consensus is reached. Exxact solution enables faster, more accelerated product development via improved hardware. We also want to deliver some key methods and technologies that facilitate prototyping, enabling companies like yours to stay ahead of the curve.
Leveraging AI & machine learning
Successful product development starts with a well-defined idea, goals, and design, forming the foundation of the entire project. The developmental stage is a personal and human task. Regardless, AI can assist in unique ways.
Predictive analysis
While this step should have already been assessed before the product development endeavor, machine learning algorithms like Time Series Analysis can analyze the market demand. This early-stage market research helps validate the product in the early stages of production.
AI-driven design
While AI cannot help ideate and create an invention, it can help in the design process. Visually, AI tools can help designers iteration variations with the ease of a prompt-based generative AI, creating unique patterns that can brand the company.
Drawing and ideating is the most human form of bringing thoughts to paper. A product always starts off with a sketch which can be prompted into a generative AI to create realistic renders. While renderings may not end up in the production model of your product, they can influence a product’s design elements and considerations and provide a starting point for further design process.
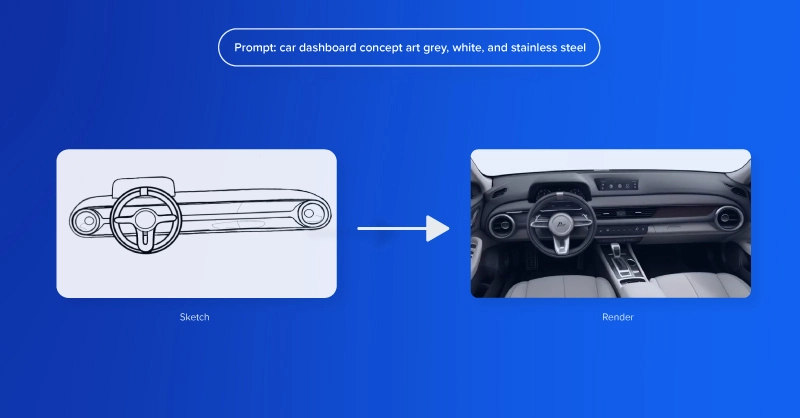
On the quantitative side, AI and Machine Learning Algorithms are excellent at solving optimization problems. Alongside simulation workflows, utilizing an ML model to adjust parameters to optimize outcomes can prove extremely useful and quick.
Automation
AI tools have emerged in simulation workflows for automating repetitive tasks. Updates to models can be immediately simulated to accelerate results. Automation can also optimize the prototyping manufacturing process tasking 3D printers or CNC machines to push iterative parts out faster.
Accelerating prototyping with optimized GPUs and hardware
Applications for simulation, rendering, and analysis first were programmed to run on CPUs only. GPU-accelerated general-purpose computing is quite young, about 10-15 years old since the introduction of the CUDA for programming NVIDIA GPUs. Although 10-15 years seems like an extremely long time in the tech industry, it is still making breakthroughs. Fluid simulation, rendering, and CAD-based applications are making the move towards GPU acceleration within the last 3-5 years.
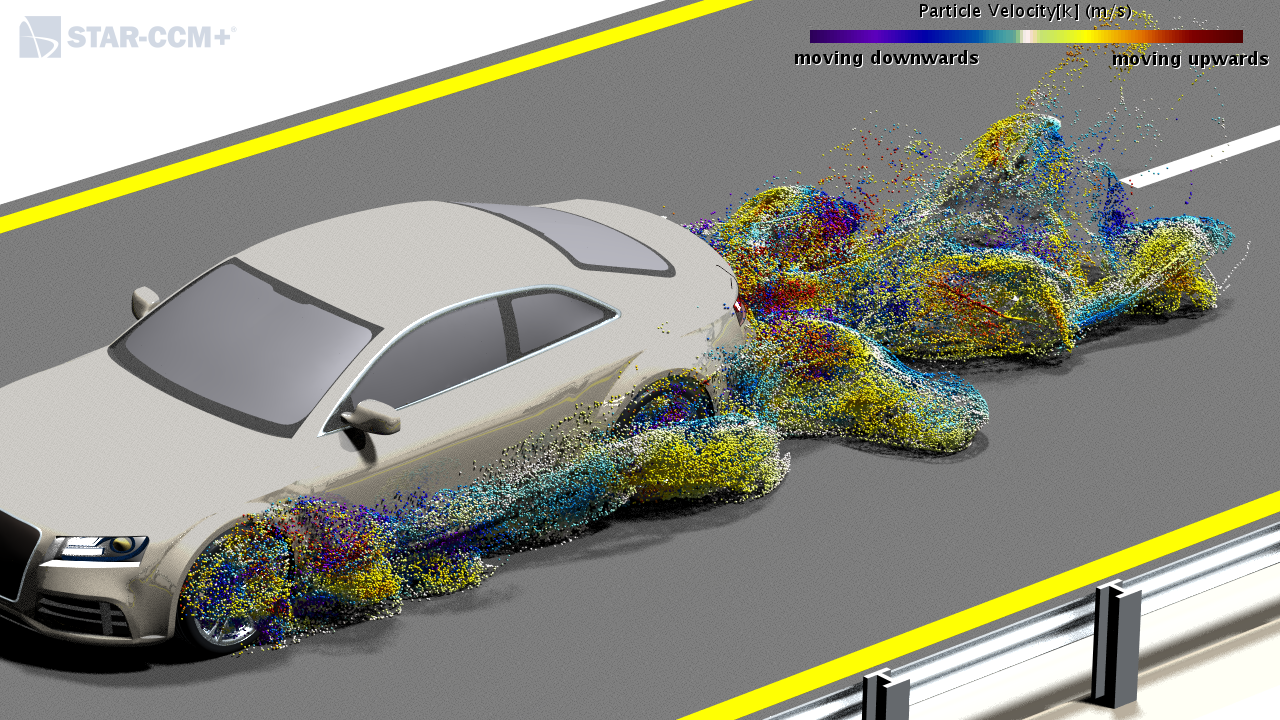
CAD and real-time visualization on GPUs
Designing 3D prototyping models in CAD software like Siemens NX, Dassault SOLIDWORKS, and more is an essential workflow. High-performance GPUs enable a smoother CAD modeling experience for a more enjoyable modeling experience, especially in high polygon designs. We recommend a system with a high core count CPU with ample RAM, as well as a high-performance GPU like the RTX 4090 or RTX 5000 Ada. GPUs with more memory let you store the model in fast memory for quicker and smoother manipulations.
Rendering and simulations
Often, product design requires simulation, especially when developing vehicles or airflow where aero is a key component in designing a part. Rendering and simulations can take multiple hours or even days on a high-fidelity model using CPU-based solutions. However, many CFD solvers like Ansys Fluent, STAR-CCM+, and PowerFlow have adopted GPU acceleration to achieve faster solve times.
High-performance GPUs allow quicker assessment to simulate an environment that mimics the real-world scenario. For example, aerospace engineers simulate crash tests or aerodynamic performance in a fraction of the time with powerful GPUs compared to CPU-only, which lets them optimize the design parameters more quickly and efficiently.
A concern some engineers may have is the accuracy of these solvers on GPUs but with ample testing, Exxact has found little deviation when simulating CFD models on CPUs vs GPUs. Exxact recommends GPUs with large memory sizes such as the NVIDIA RTX 6000 Ada 48GB for workloads that can calculate on single precision or the NVIDIA A800 40GB Active for double-precision workloads.
Digital to physical – 3D printing and augmented reality
Bringing a prototype model from digital to physical is an important step to finalizing the visual and physical feel of the product. A company can create a working prototype using the exact material but there are numerous ways to approach preproduction models including 3D printing and AR that cut cost and time. Both these methodologies require robust GPU-accelerated hardware for CAD modeling and running smooth graphics within the VR/AR headset.
3D printing
3D printing technology inspired the creation of rapid prototyping as a concept while other manufacturing techniques like injection molding and CNC machining can be used for rapid prototyping. 3D printing remains one of the most suited for this process.
Recent advancements in 3D printing materials and processes have expanded the possibilities for prototyping. With multi-material 3D printers for resin, metal, and thermoplastics, it’s now possible to create pre-production prototypes that closely resemble the final product. This capability allows designers to fine-tune the hand feel of their product before moving on to full-scale production, ensuring that the final design meets all requirements.
Virtual and augmented reality
Advancements in technology are opening the door for innovative prototyping methods. Prototyping using emerging technologies such as Virtual Reality(VR) and Augmented Reality(AR) have already been transforming the way designers and engineers work with prototypes.
With VR, designers can interact with a virtual prototype by creating an immersive environment, allowing detailed inspections of product features, spatial relationships, and functionality without the need for a physical model. Similarly, AR can overlay the virtual 3D prototypes onto the physical environment, allowing them to inspect how a product would look and function in the intended environment. For example, car manufacturers utilize augmented reality to test ergonomics inside a vehicle’s cabin.
Conclusion
In today’s competitive market, accelerating the prototyping process helps companies to stay ahead of the curve. Everyone from designers and engineers to stakeholders is now on a single, unified path. Integrating cutting-edge technologies such as AI-driven design, 3D printing, AR/VR, and leveraging powerful computing resources like high-end GPUs to drastically reduce the time from concept to final product.
Investing in the appropriate HPC hardware allows for quicker iterations, improves decision-making, and even streamlines user testing. Thus reducing not only the time-to-market but also aligning your product with market needs and quality expectations.